Handmade or hand-selected, we're proud to support exquisite craftsmanship and specialist skills. Join us as we sit down with artisans, curators, and designers in our Meet The Designer series.
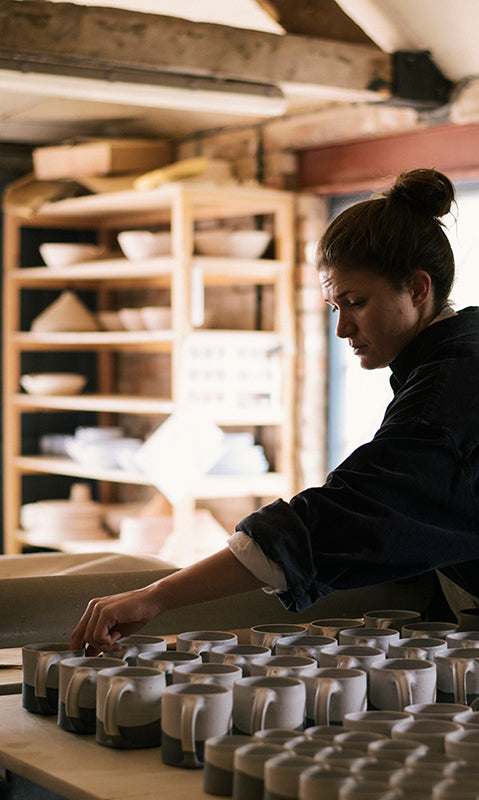
Pioneers of quality craftsmanship, British manufacturers deVOL has evolved from trusted kitchen brand to innovative design house. Now producing a varied collection of beautiful yet practical objects for the home, deVOL has built a team of talented artisans who hand develop this bespoke range of hardware, kitchenware, and lighting for the home. Their simple, utilitarian forms complementing the classic English designs the brand is known for. Here we meet the makers of deVOL's Cotes Mill studio to learn more about their process and the benefit of buying handmade.
Claire Fowler, Potter
What inspires the form of the deVOL kitchenware collection?
The forms of the kitchenware collection are mostly inspired by the need for them to be practical. I have always made functional pottery, so I like to keep each item unfussy and modest. I have taken inspiration from both classic and contemporary ceramics and tried to find a balance so that the range has a timeless quality.
What informs your choice of colour?
Whilst at university my initial colour choices were informed through extensive testing of handmade coloured clays. Creating a vast body of research allowed me to pick a suitable colour palette to work with during my final year, which was when I started collaborating with deVOL.
What is the benefit of buying handmade over mass produced?
With the recent revival of crafts and studio pottery, in particular, becoming increasingly popular, consumers are becoming more mindful of the products they buy, choosing quality over quantity in the fast-paced and mass-manufactured world we live in. I think the ever-growing desire for authenticity and the appreciation of imperfection means handmade products, like the deVOL kitchenware collection, are ever more appealing because everything is designed and made by hand in our pottery studio.
Could you explain your process when making these pieces?
I throw all the tableware in batches of 20 to 30 concentrating on one product at a time. Once thrown, it is left to firm until it is dry enough to handle without deforming the piece. It is then trimmed and left to dry completely before the first firing. There are two firings; the first is called a bisque firing and fires to 1000°C to remove any remaining water from the clay and turn it into porous ceramic to allow glaze to be applied. Once glazed, the kitchenware goes through a second firing to 1240°C, which melts the glaze and makes the work functional and food safe.
It’s really rewarding for me as a maker to see the kitchenware collection, and all the other ceramic products I make, transform from a bag of clay in the studio into finished products displayed in our showrooms. They become real objects and possessions that our customers can cherish and use in their everyday lives.
Kat Major, Ceramicist
What inspired the porcelain collection and the forms that feature within it?
I joined the deVOL accessories team just as the lower mill house renovations started. Our Creative Director, Helen, had plans to transform this space into a bright and airy kitchen by using a lot of white complimented by rich dark woods, terracotta floors and the odd bit of greenery. As porcelain clay is so perfectly white it is its purity and translucent nature that made it the obvious material to use for the new pendant range.
The forms used in the collection are very simple. I didn't set out with a specific idea or shape in mind, most of the designs came about through trial and error. I made countless prototypes based on all kinds of forms I had seen before, old and new. This meant that the final collection ended up including 14 varying designs - so there's something for everyone!
Could you explain your process when working with porcelain?
I have two main making processes - the pleated pendants are formed by laying a thin slab of porcelain over a slump mould. This is then carefully pressed down to form the initial shape of each light before trimming and finishing. The rest of the collection is hand thrown on the wheel and when the shades are leather-hard they are turned and burnished slightly to achieve a smooth, clean surface.
How is the ‘chattered’ pattern achieved?
Chattering is a repetitive surface decoration technique that has been used on wheel-thrown wares for centuries. It is created by allowing a sharp metal tool to bounce rhythmically on the surface of the pot whilst the wheel spins. The overall look is changeable as the pattern is determined by factors such as the speed of the wheel, the length, and flexibility of the tool and the density of the clay.
What tools do you work with?
I have a very small collection of tools. When throwing all I need is a sponge and a bevelling tool before wiring the pot off. I use a few more when turning - I have a very sharp loop tool that is best for chattering and a softer-edged loop tool which is great for smoothing the surface of the plain shades. I then use a rubber rib to burnish the surface slightly, and that's it!
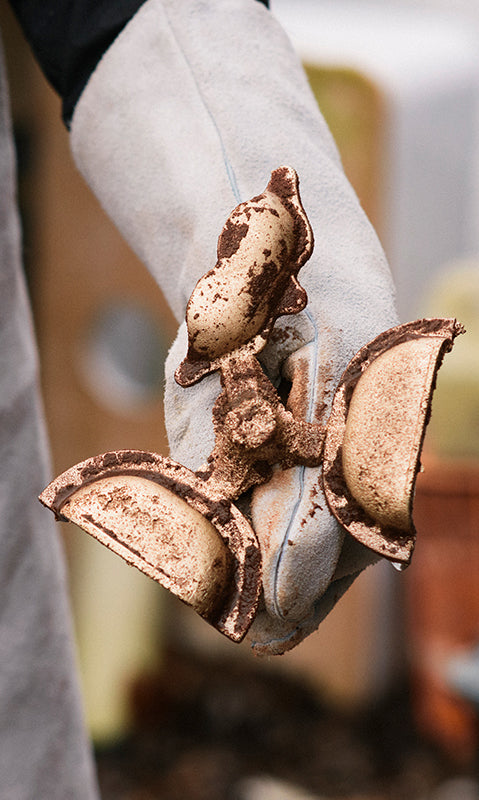
Stephanie O'Leary, Jeweller, and Metalsmith
Could you explain a little about your process when designing metalware pieces?
The process always starts with a scribble, an idea that is developed and slowly refined. I like to ‘draw’ in 3D as early on in the process as possible by modeling something quickly out of a lump of clay - you just can’t beat being able to hold and manipulate a material with your hands. The final design is then carved out of wax, modeled up in Blender and 3D printed to produce a master pattern. These are then used to make a mould ready for sand casting!
What makes finishing touches such as these so important?
Often what distinguishes the style of a kitchen and ties a whole look together is the hardware. Here at deVOL, we don’t want to use any old standard knobs and handles on our kitchens, and it’s often difficult finding the ‘perfect’ product that you’ve visualised in your head for so long. So instead we decided to materialise it ourselves and re-design our own.
It makes sense that every aspect of a deVOL kitchen, right down to the handles, should be equally well designed and made by deVOL. Good design is all about equal consideration for every aspect: form, aesthetic and utility. The quality of deVOL is in their attention to detail, the last finishing touches.
What does a typical day look like for you?
I’ve been working at deVOL for about 18 months now and the best part about my job is that there are no typical days! I now manage such a diverse range of handmade metal products that every day is as hectic and varied as the next.
Having said that, you’ll usually find me in the metals studio casting and applying various finishes to all of our handcrafted metalware products, such as the knobs and handles, aged brass accessories and even the copper fabricated worktops. In fact, our handles have been so popular lately that we’ve hired an assistant to keep up with production demands.